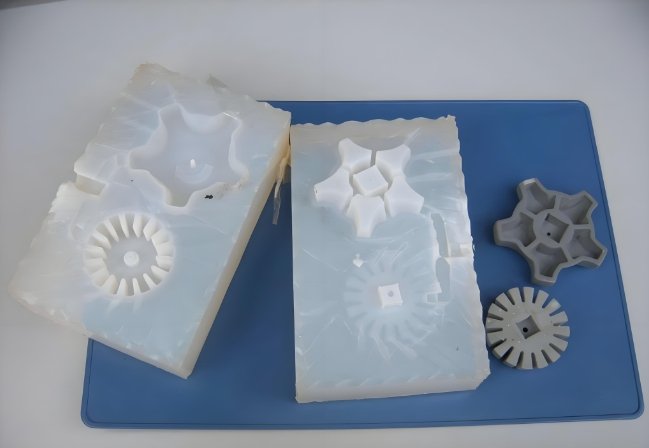
Prototyping is crucial in product development. It tests ideas before mass production. Rapid prototyping and traditional prototyping serve this purpose differently. Both have pros and cons. Understanding their differences helps in choosing the best option.
What is Traditional Prototyping?
Traditional prototyping uses manual methods. These include carving, casting, or machining. The process is slow and labor-intensive. It often involves multiple revisions. Materials like wood, metal, or clay are common.
What is Rapid Prototyping?
Rapid prototyping uses advanced technology. Examples include 3D printing, CNC machining, and injection molding. It quickly creates models from digital designs. An injection mould company plays a big role in this process.
Speed of Production
Rapid prototyping excels in speed. It creates prototypes in hours or days. Traditional methods take weeks or months. For time-sensitive projects, rapid prototyping is ideal.
Cost Differences
Traditional prototyping can be costly. Labor and material expenses add up. Rapid prototyping minimizes these costs. It uses less material and automates production. An injection mould company ensures affordability.
Material Usage
Traditional methods rely on specific materials. This limits flexibility. Rapid prototyping allows for a wider range. These include plastics, resins, and metals. An injection mould company provides access to diverse materials.
Accuracy and Precision
Traditional prototyping may lack precision. Manual methods leave room for error. Rapid prototyping ensures high accuracy. Digital designs reduce mistakes. An injection mould company ensures perfect results.
Ease of Revisions
Revisions are harder in traditional methods. Changes mean starting over. Rapid prototyping simplifies this. Digital files are easily updated. An injection mould company supports quick revisions.
Complexity of Designs
Traditional methods struggle with complex designs. Rapid prototyping excels here. It easily handles intricate shapes. This makes it perfect for innovative products.
Scalability
Traditional prototyping is best for single models. Scaling up is difficult. Rapid prototyping supports both small and large batches. An injection mould company ensures smooth transitions to production.
Applications in Different Industries
- Traditional Prototyping: Ideal for art, sculpture, and one-off projects.
- Rapid Prototyping: Dominates tech, healthcare, and automotive sectors. An injection mould company meets industry-specific needs.
Environmental Impact
Traditional methods generate waste. Rapid prototyping is more eco-friendly. It uses less material. Processes are more efficient.
Accessibility
Traditional methods need skilled artisans. This limits availability. Rapid prototyping is widely accessible. Advanced tools make it easier to adopt. An injection mould company ensures accessibility worldwide.
Case Studies
- Automotive Sector
A car company used rapid prototyping for a new engine part. It saved months in development. An injection mould company provided precise molds. - Medical Field
A startup created prosthetics using rapid prototyping. It achieved accuracy and cost savings. Traditional methods were too slow.
Challenges of Rapid Prototyping
- Initial investment in equipment.
- Learning curve for new tools.
- Limited material strength for some processes.
However, partnering with an injection mould company overcomes these issues.
Challenges of Traditional Prototyping
- High costs.
- Time-consuming processes.
- Limited flexibility in design.
These drawbacks make rapid prototyping the preferred choice.
Why Choose Rapid Prototyping?
- Faster turnaround times.
- Cost-effective solutions.
- Precise and flexible designs.
- Easier scalability.
An injection mould company ensures these benefits.