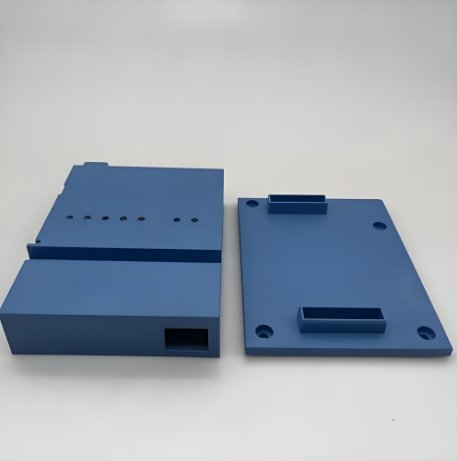
When planning your next housing injection molding project, one of the first and most critical choices is whether to use a single-cavity or multi-cavity mold. This decision directly affects tooling cost, production speed, part consistency, and scalability.
A skilled Mold Maker will evaluate your goals, part complexity, and expected volume before recommending the right mold configuration. In this article, we’ll explore the key differences between single-cavity and multi-cavity molds for plastic housings. We’ll also explain how each option performs across performance, cost, and quality metrics.
What Is a Single-Cavity Mold?
A single-cavity mold produces one housing part per injection cycle. It contains one impression of the product.
In housing injection molding, single-cavity molds are often used for:
- Low-volume production
- Prototyping and testing
- Highly complex or large housings
- First-run manufacturing before scaling
A professional Mold Maker will design the mold with excellent gating, cooling, and ejection systems to ensure each cycle produces one perfect housing.
What Is a Multi-Cavity Mold?
A multi-cavity mold has multiple identical impressions of the same housing part. It produces multiple parts per cycle—2, 4, 8, 16, or more.
In high-volume housing injection molding, this is the go-to choice for reducing part cost and improving efficiency. A trusted Mold Maker will carefully balance the mold layout to ensure even flow to all cavities.
Key Differences: Single vs. Multi-Cavity Molds
Let’s look at how these mold types compare across six important factors.
1. Tooling Cost
Single-cavity molds are less expensive to produce. They require:
- Less steel
- Simpler machining
- Shorter design time
This makes them ideal when your budget is tight or you’re not sure if the product will go to mass production.
Multi-cavity molds are more complex and expensive. Your Mold Maker must ensure perfect symmetry, flow balance, and part ejection across all cavities. However, this upfront cost can be offset by lower per-part costs later.
Winner for low budget: Single-cavity
Winner for long-term savings: Multi-cavity
2. Production Speed
Multi-cavity molds win when you need fast output. If your mold has 8 cavities, one cycle gives you 8 housings. This dramatically shortens lead times and increases daily part totals.
In housing injection molding, this is key when demand is high, and time-to-market matters.
Single-cavity molds are slower but consistent. You only get one part per shot, making them better suited for short runs.
Winner: Multi-cavity
3. Part Consistency
Consistency depends on mold design. In single-cavity molds, there’s only one flow path, so the melt fills evenly every time. This makes it easier for a Mold Maker to fine-tune the mold and get highly consistent parts.
In multi-cavity molds, if the runner system isn’t well-balanced, parts may fill unevenly, causing:
- Short shots
- Flash
- Warping
- Dimensional variation
That’s why working with an experienced Mold Maker is critical. They must perform detailed flow analysis and simulate how plastic flows through the mold to each cavity.
Winner for simplicity: Single-cavity
Winner with expert design: Multi-cavity
4. Part Cost
This is where multi-cavity molds shine. Once the tool is built, each cycle delivers multiple parts. That reduces:
- Labor cost per part
- Cycle time per unit
- Machine operating cost
Over thousands or millions of units, your cost-per-piece drops significantly.
Single-cavity molds don’t benefit from this economy of scale. You pay more per part even though your tooling cost is lower.
For efficient housing injection molding, a multi-cavity mold built by a skilled Mold Maker usually results in the lowest overall part cost.
Winner: Multi-cavity
5. Flexibility and Risk
Single-cavity molds are great for design changes. If your housing shape or wall thickness needs to change, the modification is cheaper and simpler. There’s only one cavity to rework.
With multi-cavity molds, any change must be duplicated across all cavities. That means:
- Higher rework costs
- Longer lead time for revisions
- More risk if the design isn’t finalized
So, if your product is still evolving, stick with a single-cavity mold until you’re confident. Many companies begin with single-cavity tools and upgrade to multi-cavity once production is stable.
Winner for flexibility: Single-cavity
6. Lead Time for Mold Delivery
A single-cavity mold is faster to design and build. On average, it takes 3–6 weeks depending on complexity.
A multi-cavity mold may take 6–10 weeks or more, especially if your housing design includes:
- Tight tolerances
- Thin walls
- Insert molding or overmolding
That’s why your Mold Maker should always review your timeline and help you choose the right strategy.
Winner for speed to market: Single-cavity
Summary Table: Single vs. Multi-Cavity
Feature | Single-Cavity | Multi-Cavity |
---|---|---|
Tooling Cost | Low | High |
Output Speed | Slow | Fast |
Part Consistency | Very High | High (with expert design) |
Part Cost | Higher per unit | Lower per unit |
Flexibility | High | Low |
Lead Time | Shorter | Longer |
Choosing the Right Mold Strategy
Your ideal choice depends on these questions:
- Is this a prototype or full production run?
- Will the part design change?
- How many housings do you need monthly?
- What’s your timeline and budget?
- Do you plan to scale in the future?
A professional Mold Maker can walk you through these questions and offer data-backed guidance.
In many cases, the best strategy is to start with a single-cavity mold to test and finalize your design. Once stable, move to a multi-cavity mold to reduce cost and meet demand.
This two-step approach keeps your housing injection molding both flexible and cost-effective.
The Role of a Mold Maker
No matter which path you choose, a skilled Mold Maker is your most valuable partner. They can:
- Analyze flow and shrinkage
- Recommend proper gate location
- Design efficient runner systems
- Ensure part ejection and cooling work flawlessly
Whether for single or multi-cavity molds, expert craftsmanship ensures success in every stage of housing injection molding.
Final Thoughts
Both single-cavity and multi-cavity molds have their place in housing injection molding. Your decision should reflect your current needs, future plans, and available budget.
If your housing part design is stable and volumes are high, a multi-cavity mold from a trusted Mold Maker is often the smartest investment.
If you’re still prototyping or only need small batches, begin with a single-cavity mold to reduce risk and speed development.
In either case, the choice of your Mold Maker is just as important as the mold type. Choose a partner with the experience, technology, and support to deliver precision tools that power your plastic housing success.