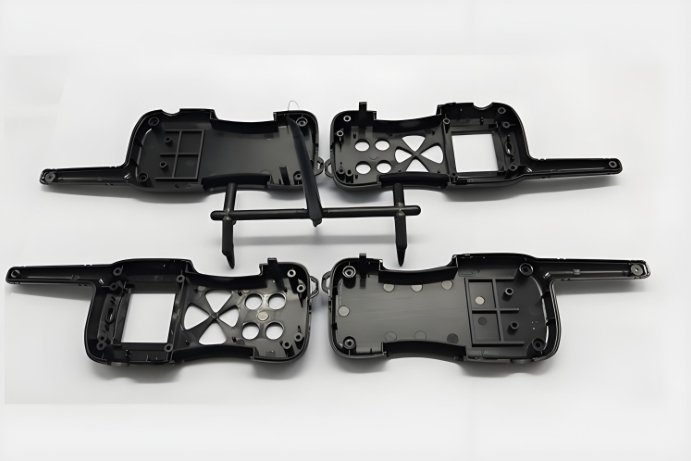
In today’s manufacturing world, housing injection molding is moving toward faster, smarter, and more precise production. At the center of this shift are smart molds—tools built with automation features and sensor-based intelligence. These molds, combined with expert input from an experienced mold maker, can bring big benefits in quality, efficiency, and cost savings.
If you design plastic housings for electronics, appliances, medical devices, or industrial tools, you need to understand how these technologies work. This article will explain how smart molds and automation are shaping the future of housing injection molding and how a professional mold maker can make that future a reality.
What Is a Smart Mold?
A smart mold is a high-tech version of a traditional injection mold. It is designed with built-in sensors, data collection tools, and control features. These additions allow real-time monitoring of things like:
- Mold temperature
- Injection pressure
- Cooling flow
- Mold open/close cycles
- Ejection force
By gathering this information during every cycle, the smart mold can help the mold maker and machine operator correct issues immediately. That means fewer defects, less scrap, and better-quality parts.
In housing injection molding, where tolerances are tight and surface finishes are critical, this level of control is extremely valuable.
Key Automation Features in Housing Molds
The automation features in smart molds go beyond just sensors. Modern mold makers now design molds that include:
1. Automatic Core Pulls and Slides
These help shape undercuts and complex interior features in plastic housings. With automation, movement happens smoothly and without delay.
2. Hydraulic or Servo Actuation
Some parts of the mold can be powered by servo motors, giving more control over movement speed and position. This leads to higher accuracy.
3. Ejection Monitoring Systems
Ejector pins are essential to remove molded housings from the tool. Smart ejection systems monitor force and pin position to prevent damage.
4. In-Mold Sensors
Temperature and pressure sensors inside the mold cavity give feedback for perfect molding conditions. A skilled mold maker uses this data to optimize part quality.
5. Hot Runner Controls
A hot runner system helps control the flow of melted plastic into the mold. With smart controls, you avoid problems like cold spots or flow marks in the housing surface.
Why Automation Matters in Housing Injection Molding
Plastic housings are often used in electronics, where looks and fit are critical. Even a small defect can cause product failure or bad user experience. That’s why automation in housing injection molding is not a luxury—it’s becoming a must.
Here’s what automation offers:
1. Consistency and Precision
Automated molds keep every cycle the same. With sensors, the mold can adjust to tiny changes in the machine or environment. This results in consistent part size and shape.
2. Faster Cycle Times
Automation reduces the time between shots. Ejection, mold movements, and core pulling all happen quicker and more reliably.
3. Lower Labor Costs
Smart molds require fewer manual checks. Some systems can even shut down automatically if they detect a problem. This lowers labor needs and human error.
4. Better Use of Data
Sensor data gives the mold maker and production team insights into how the mold performs over time. That makes it easier to do maintenance or catch problems early.
Role of the Mold Maker in Smart Mold Design
The job of the mold maker is more important than ever in this high-tech environment. A good mold maker doesn’t just cut steel—they think ahead, plan for automation, and make sure the tool supports both the product and the process.
Here’s how a skilled mold maker adds value:
- Understands housing requirements: Size, wall thickness, mounting points, texture—all must be molded perfectly.
- Knows which sensors to use: Not all applications need full automation. The mold maker chooses the right balance.
- Designs for long-term use: Automated molds are often used in high-volume jobs. A strong design ensures durability.
- Supports setup and training: Many mold makers now help with installation and operator training.
The best mold makers work as partners—not just vendors. They help clients reach goals faster with fewer risks.
Applications of Smart Molds in Housing Production
Smart, automated molds are especially useful in industries where housing performance is tied to safety or customer satisfaction. Key areas include:
- Consumer electronics – Housings for phones, smart home devices, or wearables
- Medical devices – Plastic enclosures for diagnostics, pumps, or monitoring tools
- Automotive – Dashboard parts, sensor covers, or switch housings
- Industrial equipment – Enclosures for control panels, meters, or hand tools
In each case, the requirements are similar: high precision, repeatability, and clean appearance. Smart molds make this level of performance possible.
Challenges and Considerations
While the benefits of smart molds are clear, it’s important to consider the challenges as well.
- Upfront cost: Automation adds to the mold price. A good mold maker will explain the return on investment over time.
- Maintenance: Sensors and moving parts need upkeep. Choose a mold maker who offers support and spare parts.
- Training: Operators need to learn new systems. Fortunately, many smart mold systems are user-friendly.
The key is to plan carefully and work closely with an experienced mold maker who understands your goals and product needs.
The Future of Housing Injection Molding
As manufacturing becomes smarter, housing injection molding will continue to evolve. Expect to see more integration between mold sensors, production software, and quality systems. Eventually, factories will use real-time mold data to control the entire line automatically.
Mold makers who adapt to this change will become trusted advisors in smart manufacturing. They will build not just tools, but full solutions that improve product quality, reduce costs, and shorten time to market.
Conclusion
Smart molds with automation features are revolutionizing housing injection molding. By using advanced sensors, data tracking, and mechanical automation, companies can achieve higher quality, speed, and cost control.
To succeed, you need a forward-thinking mold maker who understands these technologies. The best mold makers don’t just build molds—they design smart systems that power the future of plastic housing production.
If you’re planning your next housing project, talk to a mold maker who offers smart mold solutions. It could be the smartest decision you make for your product’s success.