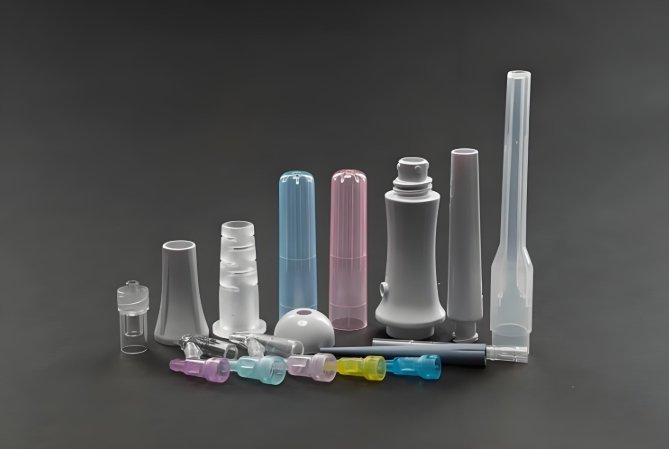
Medical devices must be safe and clean. They undergo sterilization to remove bacteria. Medical injection molding uses special plastics that resist sterilization methods. A skilled mold maker selects the best material. The right plastic ensures durability and compliance with medical standards.
1. Why Sterilization-Resistant Plastics Matter
Ensuring Patient Safety
Medical devices must be germ-free. Proper sterilization prevents infections.
Maintaining Material Strength
Heat, radiation, and chemicals can weaken plastics. Resistant materials maintain their properties.
Regulatory Compliance
Medical plastics must meet strict FDA and ISO standards. They must pass sterilization tests.
Long-Term Performance
Reusable medical devices need repeated sterilization. The right plastic ensures a long lifespan.
2. Common Sterilization Methods in Medical Injection Molding
1. Autoclave (Steam Sterilization)
- Uses high heat and pressure.
- Effective but can degrade some plastics.
2. Gamma Radiation
- Uses high-energy rays to kill bacteria.
- Can affect the strength of some materials.
3. Ethylene Oxide (EtO) Sterilization
- Uses gas to sterilize heat-sensitive devices.
- Some plastics absorb gas and need aeration.
4. Chemical Sterilization
- Uses disinfectants like hydrogen peroxide.
- Works for heat-sensitive materials.
3. Best Plastics for Sterilization in Medical Injection Molding
1. Polycarbonate (PC)
- High impact strength.
- Resists gamma and chemical sterilization.
- Used in surgical instruments.
2. Polypropylene (PP)
- Lightweight and flexible.
- Handles autoclave sterilization.
- Common in syringes and containers.
3. Polyether Ether Ketone (PEEK)
- Extreme heat and chemical resistance.
- Withstands repeated autoclaving.
- Used in implants and surgical tools.
4. Polysulfone (PSU)
- Transparent and tough.
- Resists heat and chemical sterilization.
- Used in filtration and diagnostic devices.
5. Polyvinyl Chloride (PVC)
- Flexible and cost-effective.
- Handles EtO and chemical sterilization.
- Common in tubing and IV bags.
6. Acrylonitrile Butadiene Styrene (ABS)
- Tough and lightweight.
- Works with gamma and EtO sterilization.
- Used in medical housings and enclosures.
7. Silicone
- Soft and biocompatible.
- Withstands autoclave and chemical sterilization.
- Used in catheters and implants.
4. How a Mold Maker Ensures Sterilization Compatibility
Testing Material Resistance
Plastics undergo sterilization testing. They are exposed to heat, chemicals, and radiation.
Assessing Device Functionality
A mold maker ensures the plastic maintains its shape and strength. Medical devices must work after sterilization.
Considering Repeated Sterilization
Some devices need multiple sterilization cycles. The mold maker selects materials that last.
Regulatory Compliance Checks
The mold maker follows FDA, ISO, and USP Class VI standards. This ensures medical safety.
5. Challenges in Selecting Sterilization-Resistant Plastics
Material Degradation
Not all plastics withstand high temperatures or chemicals. Choosing the wrong one leads to cracks or discoloration.
Cost Considerations
Some sterilization-resistant plastics are expensive. The mold maker balances cost and performance.
Sterilization Method Compatibility
A material that works for one method may fail in another. Proper selection is critical.
Regulatory Hurdles
Meeting medical regulations takes time. Testing and certification add to production time.
6. Applications of Sterilization-Resistant Plastics
Surgical Instruments
Tools made from polycarbonate and PEEK last through multiple sterilizations.
Implants and Prosthetics
PEEK and silicone implants must endure body conditions and sterilization.
IV and Drug Delivery Systems
Polypropylene and PVC ensure safe fluid transfer.
Diagnostic Equipment
ABS and polysulfone housings withstand gamma and chemical sterilization.
Medical Packaging
Sterilized plastic packaging keeps tools germ-free.
7. The Role of Medical Injection Molding in Sterilized Devices
Step 1: Material Selection
A mold maker picks the best plastic for sterilization methods.
Step 2: Mold Design
The mold ensures precise part formation.
Step 3: Injection Molding Process
Plastic is melted, injected, and shaped.
Step 4: Quality Control
Each part is tested for strength and sterilization resistance.
8. Future Trends in Sterilization-Resistant Plastics
Biodegradable Medical Plastics
New materials reduce medical waste while maintaining sterility.
Advanced Polymers
Stronger, lighter plastics improve device durability.
Smart Materials
Some plastics can self-sterilize, reducing contamination risks.
Sterilization-resistant plastics are vital for medical injection molding. A skilled mold maker ensures material safety, durability, and compliance. With the right plastic, medical devices remain sterile, strong, and effective.