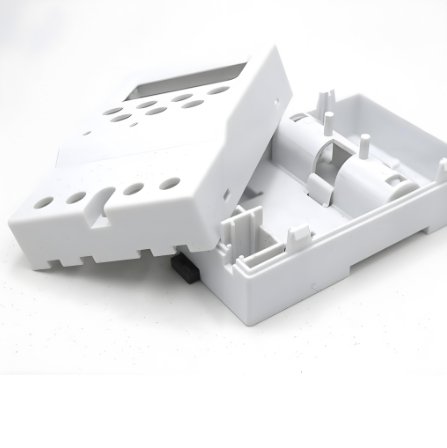
Choosing the right tooling material is critical in Electronic Injection Molding. A skilled Mold Maker understands this well. The material affects mold life, part quality, and cost. It also affects how fast and how often a mold can run.
In this article, we’ll explore the best tooling materials. We’ll also look at how a Mold Maker picks the right one. We’ll discuss benefits, challenges, and how to make smart choices. This is key for high-quality electronic parts.
Why Tooling Material Matters in Electronic Injection Molding
Tooling material directly affects product quality. Electronic parts need tight tolerances. Any deformation or error can cause failure. A good mold must resist wear and heat. It must also hold shape for many cycles. The right material helps achieve this.
A good Mold Maker balances strength, cost, and performance. They choose materials based on part design, production volume, and resin type.
Key Properties for Tooling Materials
Before choosing, the Mold Maker checks key factors:
- Hardness
- Thermal conductivity
- Corrosion resistance
- Wear resistance
- Dimensional stability
Each of these affects mold life and part accuracy. In Electronic Injection Molding, these properties matter a lot.
P20 Steel – A Popular Choice
P20 tool steel is widely used. It offers a good balance. It’s pre-hardened. This means less time in heat treatment. It has decent hardness and toughness.
It’s great for medium-volume production. A Mold Maker uses it when cycles are around 50,000–100,000. It also machines easily. That saves time and cost.
But it’s not good for abrasive resins. It may wear fast in such cases.
H13 Steel – For High Heat and Strength
H13 tool steel is a premium option. It handles high temperatures well. It also resists wear. That makes it perfect for glass-filled or flame-retardant plastics.
It’s ideal for long runs. A Mold Maker may use H13 when the mold needs to last 500,000+ cycles. It keeps shape under stress. It also resists thermal shock.
But it’s more expensive. And harder to machine. So it’s used for critical, high-value parts.
S7 Steel – Shock Resistant and Tough
S7 tool steel offers great toughness. It’s good for molds that take impact or sudden loads. It also works well with abrasive materials.
In Electronic Injection Molding, S7 is great for inserts and cores. A Mold Maker uses it when toughness is more important than hardness.
However, S7 is not ideal for high-heat resins. It may deform over long cycles.
Stainless Steels – For Corrosive Resins
Some electronic parts use corrosive plastics. These include PVC or flame-retardant grades. In such cases, stainless steels are preferred.
Grades like 420 or 440C are common. These resist rust and chemicals. A Mold Maker selects them when rust could affect part quality.
Stainless molds also suit cleanroom conditions. But they are harder to machine. And often cost more. So they’re used where cleanliness and corrosion resistance are key.
Beryllium-Copper – For Fast Cooling
Beryllium-Copper alloy (BeCu) has high thermal conductivity. It cools fast. That shortens cycle time. It also helps reduce warping.
BeCu is often used in core inserts or areas where cooling is hard. A Mold Maker may combine it with steel. That way, it improves cooling without compromising strength.
But BeCu is costly. It also needs special care during machining. So it’s only used where needed most.
Aluminum – For Short Runs
Aluminum molds are great for prototypes or low-volume runs. They machine fast and are less costly. They also transfer heat well, which helps with cooling.
For under 10,000 cycles, aluminum works fine. A Mold Maker may use high-grade aluminum like 7075. It offers better strength than basic grades.
However, aluminum wears out fast. It’s soft and can’t handle high pressures. So it’s not suitable for tough or high-volume jobs.
Composite Tooling – For Special Cases
Some Mold Makers use composite or epoxy tooling. These are for very low volume or test molds. They are fast to produce. They’re also cheaper than metal molds.
These tools are good for design validation. But they have low strength. They wear quickly. And they don’t work well with high temperatures.
So, they are rarely used in production Electronic Injection Molding.
Matching Tooling to Plastic Type
The plastic used also affects the tooling choice. Some resins wear down steel. Others release corrosive gases. The Mold Maker must match the mold material to the resin.
For example:
- Glass-filled resins need wear-resistant steel like H13
- PVC needs stainless steel
- Fast-cycle resins benefit from BeCu inserts
This pairing is vital. It prevents early failure. It also protects the electronic component’s shape and size.
Cost vs. Lifespan
A major decision factor is cost. High-grade materials cost more. But they last longer. A Mold Maker calculates the cost per part. This helps decide if high-cost steel is worth it.
For high-volume molds, expensive tooling pays off. For short runs, aluminum or P20 may be better. The Mold Maker makes this call based on client needs.
Precision Needs and Mold Complexity
Tooling choice also depends on the part’s complexity. Tight tolerances need stable materials. Harder steels resist distortion. That ensures dimensionally stable parts.
Complex molds may use multiple materials. For example, H13 for cavities, and BeCu for cores. This mix gives strength and fast cooling.
A skilled Mold Maker knows how to combine these materials. That ensures the best result.
Maintenance and Repair
Some tooling materials are easier to polish or repair. That affects maintenance time. A good Mold Maker chooses tooling that’s easy to work on when downtime must be minimal.
For example, P20 polishes well. H13 is harder but lasts longer. This balance is important in Electronic Injection Molding.
Material Selection is Key to Quality
Tooling material impacts every part of Electronic Injection Molding. From part quality to mold life. From cost to cycle time.
A Mold Maker studies the job, plastic, part shape, and volume. Then they choose the best material. This ensures smooth molding. It also cuts waste and defects.
For best results, trust your Mold Maker. They know how to balance cost and quality. And they choose tooling that gives top results for electronic parts.