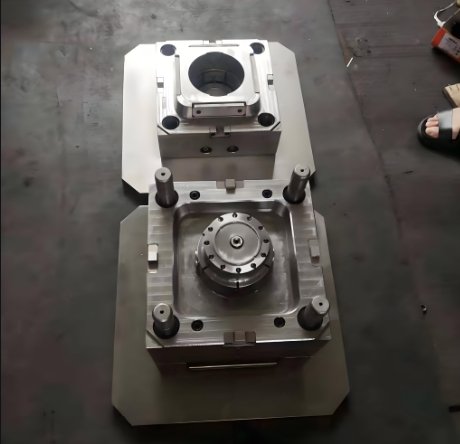
In modern product design, plastic housings are everywhere—from smartphones and routers to medical devices and smart home gadgets. These housings are not only functional but also influence how a product looks, feels, and performs. One process stands out for producing these parts quickly and accurately: Housing Injection Molding.
This guide explains the full process of Housing Injection Molding, from design and materials to tooling and production. We’ll also discuss how an expert Mold Maker helps turn a good idea into a high-quality, repeatable product.
What Is Housing Injection Molding?
Housing Injection Molding is a method used to produce plastic outer shells or enclosures for various electronic, industrial, and consumer products. These housings protect internal components, provide mounting features, and often represent the final visible surface of the product.
The process involves injecting molten plastic into a hardened steel mold. After cooling, the plastic solidifies into the shape of the cavity, forming the final housing part.
A high-quality mold, built by a skilled Mold Maker, is key to getting smooth finishes, tight tolerances, and consistent parts.
Why Use Housing Injection Molding?
There are many reasons why manufacturers choose Housing Injection Molding:
- High speed: Ideal for mass production
- Repeatability: Every part matches exactly
- Material variety: Suits many industries
- Precision: Critical for snap fits and seals
- Cost efficiency: Low cost per part in volume
With guidance from an experienced Mold Maker, this process becomes one of the most powerful tools in product manufacturing.
Step-by-Step Process
1. Design and Engineering
The design phase begins with 3D modeling. Designers must consider part thickness, support structures, snap-fit features, and assembly needs. The goal is a housing that functions well and looks good.
At this stage, input from the Mold Maker is crucial. They offer suggestions to ensure:
- Easy part ejection
- Balanced wall thickness
- No undercuts unless needed
- Proper draft angles
2. Mold Fabrication
After finalizing the part design, the Mold Maker begins building the mold. This tool is often made of hardened steel or aluminum and includes:
- Core and cavity
- Cooling channels
- Ejector pins
- Gates and runners
Precision here is critical. Any flaws in the mold will reflect in every housing produced.
3. Material Selection
Housing Injection Molding allows a wide range of thermoplastics. Common choices include:
- ABS: Good all-purpose material
- PC: High strength and clarity
- Nylon: Great for mechanical strength
- PP: Excellent chemical resistance
Each resin offers unique benefits. The Mold Maker may also advise on fillers, additives, or colorants to improve performance.
4. Injection Molding Process
Once the mold is installed in the press, the process begins:
- Plastic pellets are heated and melted.
- The molten plastic is injected into the mold.
- The material cools and hardens.
- The mold opens, and ejector pins push out the finished housing.
This cycle repeats rapidly—sometimes every few seconds. A well-built mold from a professional Mold Maker ensures minimal downtime and fewer defects.
Applications of Housing Injection Molding
This method is used across many industries:
- Consumer Electronics: Remote controls, routers, phones
- Medical Devices: Diagnostic tools, enclosures
- Automotive: Dashboard controls, sensor covers
- Industrial Equipment: Control boxes, panel covers
- Home Appliances: Blenders, fans, thermostats
No matter the application, the housing must be tough, lightweight, and dimensionally precise—all made possible through the skills of a trusted Mold Maker.
Benefits of the Process
Precision
Housing Injection Molding offers unmatched accuracy. Features like USB ports, LED openings, or screw bosses require exact measurements. A skilled Mold Maker ensures the tool delivers the required tolerances.
Strength
Plastic housings often need to support other parts or resist impact. Proper design and material choice make this possible. The Mold Maker reinforces the design with ribs or thicker sections as needed.
Appearance
Visual appeal matters. With the right mold surface treatment, housings can have a glossy, matte, or textured finish—right out of the mold. The Mold Maker controls these finishes through mold polishing and surface etching.
Durability
Injection-molded housings last long, even in harsh environments. Many are UV-resistant, waterproof, or chemical-resistant. Again, material and design choices—guided by the Mold Maker—are key.
Common Design Tips
Here are a few key design rules for Housing Injection Molding:
- Use uniform wall thickness to prevent warping
- Add draft angles for easy part removal
- Avoid sharp corners (they can crack)
- Place ribs for strength, not bulk
- Think about assembly: clips, screws, or snap fits
Every successful product results from smart design and smart tooling. The Mold Maker helps balance both.
The Role of the Mold Maker
Without a doubt, the most important partner in this process is the Mold Maker. Their role includes:
- Reviewing part designs for manufacturability
- Building a precise, durable mold
- Testing and refining the tool before mass production
- Offering ongoing support if issues arise
A good Mold Maker doesn’t just follow specs—they help improve them. They understand the nuances of part flow, cooling times, venting, and shrinkage. Their insights reduce problems, speed up timelines, and lower costs.
Challenges and How to Solve Them
Even the best designs can face problems. Here are some common ones in Housing Injection Molding, and how a Mold Maker helps fix them:
- Warping: Adjust gate location, cooling rate
- Short shots: Modify mold venting or injection pressure
- Flash: Tighten parting lines or reduce injection force
- Sink marks: Redesign thick sections or add support ribs
By working closely with a skilled Mold Maker, these issues can be resolved quickly.
Housing Injection Molding remains the gold standard for creating strong, attractive, and precise plastic housings. Its benefits—speed, accuracy, design freedom, and cost efficiency—are unmatched by other methods.
Behind every great housing project stands a reliable Mold Maker. Their work ensures the mold performs flawlessly, producing top-quality housings that look good and function even better.
If you’re developing a new product, invest in good design, good materials, and a good Mold Maker. That’s the formula for success in Housing Injection Molding.