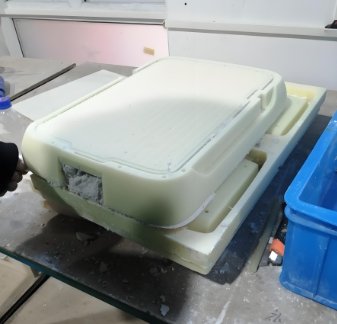
Creating custom designs can be challenging. Every project has unique requirements. This is where Rapid Prototyping excels. It offers flexibility, speed, and precision. Partnering with an Injection Mould Company enhances the process. Let’s explore why Rapid Prototyping is the best choice for custom designs.
The Need for Custom Designs
Meeting Unique Demands
Custom designs address specific customer needs. They stand out in the market.
Industry Applications
Industries like healthcare, automotive, and electronics rely on custom products.
Challenges in Traditional Methods
Conventional manufacturing struggles with flexibility. It is time-consuming and costly.
Benefits of Rapid Prototyping for Custom Designs
Flexibility in Design
Rapid Prototyping adapts to any design. It handles complex geometries easily.
Faster Turnaround
Prototypes are created quickly. This accelerates decision-making.
Cost-Effective
Traditional methods require expensive tooling. Rapid Prototyping eliminates this need.
Early Testing
Prototypes allow early testing of fit, form, and function.
Iterative Process
Designers can make changes instantly. This reduces errors.
Role of an Injection Mould Company
Material Expertise
They select materials that suit custom designs. This ensures durability.
Precision Manufacturing
Their tools ensure accurate prototypes.
Scalable Solutions
They transition prototypes into mass production seamlessly.
Applications of Custom Designs
Medical Devices
Rapid Prototyping creates prosthetics and implants tailored to patients.
Consumer Products
Custom designs improve user experience.
Automotive Parts
Prototypes test and refine unique vehicle components.
Electronics
Custom casings and connectors enhance functionality.
Tools for Custom Rapid Prototyping
3D Printing
Ideal for detailed designs. It offers high flexibility.
CNC Machining
Best for durable, functional prototypes.
Injection Molding
Perfect for complex, high-precision custom parts.
Steps in Custom Rapid Prototyping
- Define Requirements
Identify the unique aspects of the design. - Choose the Right Method
Select the most suitable Rapid Prototyping tool. - Partner with Experts
Collaborate with an Injection Mould Company. - Test Prototypes
Refine the design through multiple iterations. - Prepare for Production
Transition from prototype to final product efficiently.
Real-World Examples
Custom Prosthetics
A medical company used Rapid Prototyping to create patient-specific prosthetics. The process was fast and accurate.
Automotive Innovations
An auto manufacturer developed custom dashboard components. Prototypes underwent multiple tests for durability and design.
Electronics Enhancements
A tech startup designed a custom laptop casing. Rapid Prototyping ensured perfect fit and strength.
Advantages Over Traditional Methods
Shorter Lead Times
Prototypes are ready in days, not weeks.
Lower Costs
No expensive molds or tooling is required.
Greater Design Freedom
Complex shapes and intricate details are easily achievable.
Why Choose an Injection Mould Company
Expertise in Prototyping
They bring years of experience to the table.
End-to-End Solutions
From prototype to production, they handle it all.
Quality Assurance
Their prototypes meet the highest standards.
Industries Benefiting from Custom Designs
Healthcare
Tailored solutions improve patient outcomes.
Aerospace
Custom parts enhance performance and safety.
Consumer Goods
Unique designs attract more customers.
Rapid Prototyping is perfect for custom designs. It offers flexibility, speed, and cost-effectiveness. An Injection Mould Company plays a vital role. They bring expertise and resources to the table. Together, they deliver high-quality, tailored solutions. Embracing Rapid Prototyping ensures innovative and successful products.